Comprehending What is Porosity in Welding: Reasons and Solutions
Comprehending What is Porosity in Welding: Reasons and Solutions
Blog Article
The Science Behind Porosity: A Comprehensive Overview for Welders and Fabricators
Comprehending the elaborate systems behind porosity in welding is essential for welders and fabricators making every effort for impeccable craftsmanship. From the structure of the base products to the details of the welding process itself, a plethora of variables conspire to either intensify or reduce the visibility of porosity.
Comprehending Porosity in Welding
FIRST SENTENCE:
Assessment of porosity in welding discloses crucial understandings into the honesty and quality of the weld joint. Porosity, defined by the existence of tooth cavities or voids within the weld metal, is a common worry in welding procedures. These voids, otherwise properly attended to, can endanger the architectural integrity and mechanical homes of the weld, resulting in potential failings in the ended up product.
To discover and quantify porosity, non-destructive testing methods such as ultrasonic screening or X-ray inspection are often employed. These methods enable the identification of inner problems without compromising the stability of the weld. By examining the size, form, and circulation of porosity within a weld, welders can make educated choices to enhance their welding procedures and attain sounder weld joints.
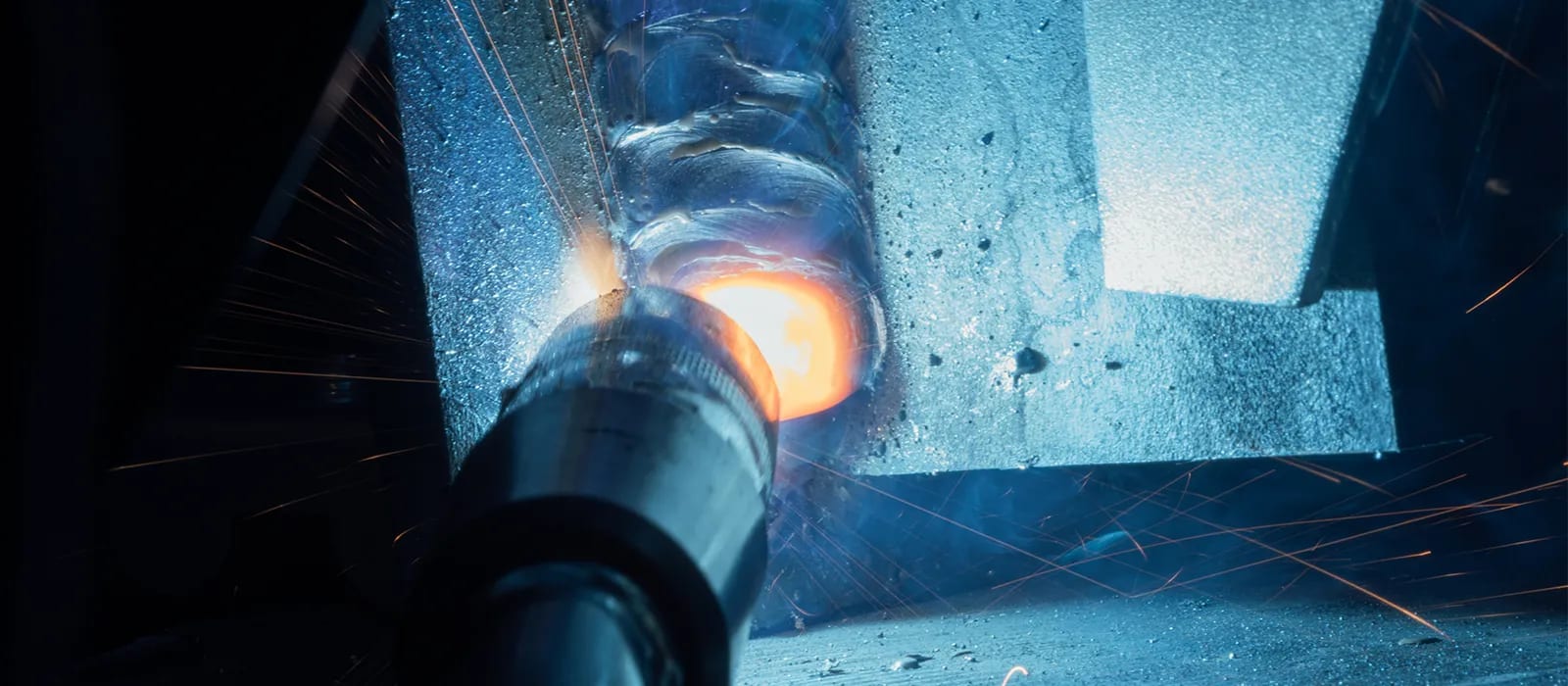
Elements Influencing Porosity Formation
The occurrence of porosity in welding is affected by a myriad of elements, ranging from gas shielding effectiveness to the ins and outs of welding specification setups. Welding criteria, including voltage, current, travel rate, and electrode kind, also effect porosity formation. The welding strategy utilized, such as gas steel arc welding (GMAW) or shielded metal arc welding (SMAW), can influence porosity development due to variations in heat distribution and gas coverage - What is Porosity.
Results of Porosity on Weld High Quality
The presence of porosity also compromises the weld's resistance to rust, as the caught air or gases within the spaces can react with the surrounding environment, leading to destruction over time. Additionally, porosity can hinder the weld's ability to endure stress or effect, more jeopardizing the general top quality and dependability of the welded framework. In crucial applications such as aerospace, automobile, or architectural building and constructions, where safety and sturdiness are vital, the harmful effects of porosity on weld high quality can have serious consequences, stressing the value of lessening porosity through correct welding strategies and procedures.
Techniques to Minimize Porosity
Additionally, using the ideal welding this content parameters, such as the appropriate voltage, existing, and travel rate, is critical in protecting against porosity. Keeping a regular arc size and angle during welding also aids decrease the likelihood of porosity.

Furthermore, choosing the right securing gas and preserving proper gas circulation prices are crucial in reducing porosity. Utilizing the suitable welding method, such as back-stepping or utilizing a weaving activity, can likewise aid disperse warm uniformly and minimize the chances of porosity formation. Lastly, guaranteeing appropriate air flow in the welding setting to get rid of any possible resources of contamination is important for attaining porosity-free welds. By carrying out these methods, welders can effectively lessen porosity and produce high-grade bonded joints.

Advanced Solutions for Porosity Control
Executing sophisticated modern technologies my link and innovative methods plays a critical role in accomplishing premium control over porosity in welding procedures. One innovative remedy is the usage of innovative gas combinations. Protecting gases like helium or a mix of argon and hydrogen can aid minimize porosity by supplying much better arc stability and improved gas coverage. Additionally, employing sophisticated welding strategies such as pulsed MIG welding or customized ambience welding can additionally help mitigate porosity concerns.
One more sophisticated service involves making use of innovative welding devices. Using equipment with integrated functions like waveform control and innovative power sources can enhance weld quality and decrease porosity risks. In addition, the application of automated welding systems with exact control over Look At This specifications can considerably decrease porosity problems.
Moreover, incorporating advanced surveillance and inspection innovations such as real-time X-ray imaging or automated ultrasonic screening can aid in finding porosity early in the welding procedure, permitting immediate restorative actions. On the whole, incorporating these advanced options can substantially enhance porosity control and enhance the general quality of welded parts.
Final Thought
In verdict, understanding the science behind porosity in welding is essential for welders and producers to produce premium welds. By identifying the elements affecting porosity formation and implementing methods to decrease it, welders can improve the general weld top quality. Advanced services for porosity control can better enhance the welding process and make certain a strong and reputable weld. It is vital for welders to continually educate themselves on porosity and carry out best methods to achieve ideal results.
Report this page